In the ever-evolving world of construction, energy efficiency and sustainability have become paramount. Building owners and designers are constantly seeking innovative ways to reduce energy consumption, enhance indoor comfort, and improve resilience to extreme weather conditions. One such approach gaining momentum is high-thermal-mass construction.
High-thermal-mass construction involves the use of materials with the ability to store heat, providing a natural way to regulate indoor temperatures.
Scope
- Climate Assessment
- Begin by determining your IECC Climate Zone to understand local climate conditions.
- Climate Suitability Analysis
- Evaluate whether high-thermal-mass construction is suitable for your climate. Consider factors such as the length of cooling and heating seasons and temperature fluctuations.
- Material Selection
- Choose high-thermal-mass construction materials like concrete masonry units (CMU), poured concrete, insulated concrete forms (ICF), stone, brick, or other masonry materials for both interior and exterior wall construction.
- Floor Material Choice
- Select high-thermal-mass materials such as concrete slabs or tile for your floors.
- Phase Change Materials (PCMs)
- Consider incorporating phase change materials (PCMs) into your design for enhanced thermal mass benefits.
- External Insulation
- Implement external insulation to minimize heat absorption by thermal mass walls and maximize their lag and damping effects.
- Thermal Bridging Minimization
- Focus on reducing thermal bridging at joints and projections to maintain the efficiency of thermal mass.
- Passive Heating and Cooling
- Integrate passive heating and cooling techniques to leverage the building-integrated thermal mass for indoor temperature regulation, particularly during extreme weather and power disruptions.
High-thermal-mass construction relies on the concept of thermal mass, which refers to a material’s ability to store heat. The greater the thermal mass, the better it can store heat. This construction technique utilizes materials with high thermal mass to stabilize indoor temperatures, providing a time lag in heat transfer between the interior and exterior and dampening indoor temperature fluctuations.
For high-thermal-mass construction to be effective, it should cover a significant area within the building and remain exposed to indoor air. This construction approach offers several advantages, such as:
- Time Lag: Indoor temperatures peak later than outdoor temperatures, enhancing comfort.
- Thermal Damping: Temperature increases are moderated, especially in regions with substantial daytime-nighttime temperature differences.
- Resilience: High-thermal-mass construction helps maintain indoor comfort during extreme heat, cold snaps, and power outages.
To maximize the benefits, it’s crucial to select appropriate materials and consider design factors like window placement to minimize unwanted heat gain. While high-thermal-mass materials like concrete have their advantages, they also present some challenges, such as space constraints and curing time.
High-Thermal-Mass Construction Materials
Concrete Masonry Unit (CMU) Construction
- Utilizes stacked hollow-core concrete blocks for walls.
- Requires insulation, ideally placed on the exterior for optimal thermal mass benefits.
Insulated Concrete Form (ICF) Construction
- Employs insulated “blocks” for poured concrete walls.
- Results in air-tight walls and minimizes thermal bridging.
Poured Concrete Wall Construction
- Offers high thermal mass with flexibility in exposing it throughout the home.
- Requires attention to form preparation and steel reinforcement.
Poured Concrete Slab Floors
- Provides substantial thermal mass for both masonry and wood-framed homes.
- Requires proper insulation to prevent thermal bridging at edges.
Rammed Earth Wall Construction
- Uses compacted natural materials like earth or gravel for walls.
- Requires soil knowledge and may not be suitable for wet environments.
Adobe Wall Construction
- Traditionally sun-dried bricks or kiln-dried options.
- Performs well in thermal and acoustic aspects but may require reinforcement in earthquake-prone areas.
Trombe Wall Construction
- Focuses on passive heating with masonry walls absorbing and releasing heat.
- Requires careful design and solar orientation.
High-Mass Interior Finishes
- Enhance thermal mass in wood-framed structures with double layers of drywall, stucco, plaster, tile, or concrete countertops.
Phase Change Materials (PCMs)
- Relatively new materials that change phase to absorb and release heat.
- Choose tested and approved PCM materials and suitable integration methods.
How to Integrate Thermal Mass Construction
Climate Considerations
- Determine your climate zone and local weather conditions.
Compliance
- Ensure compliance with building codes, above-code programs, and manufacturer instructions.
Material Selection
- Choose materials with high thermal mass for walls and floors.
Insulation Placement
- Insulate on the exterior for CMU or concrete construction to optimize thermal mass properties.
Exterior Cladding
- Select light-colored cladding for warmer climates to reflect solar radiation and enhance thermal mass.
Interior Finishes
- Use double layers of drywall, stucco, plaster, or tile to increase thermal mass benefits.
Floor Construction
- Opt for concrete slabs with proper insulation to maximize thermal mass effects.
Passive Design
- Implement passive heating and cooling strategies, considering factors like building orientation, window glazing, shading, and ventilation.
Ensuring Successful High-Thermal-Mass Construction
- Confirm climate suitability by analyzing heating and cooling season lengths and diurnal temperature swings.
- Combine thermal mass with passive cooling strategies for indoor comfort during extreme conditions.
- Ensure large-scale and direct exposure of thermal mass to indoor spaces.
Climate
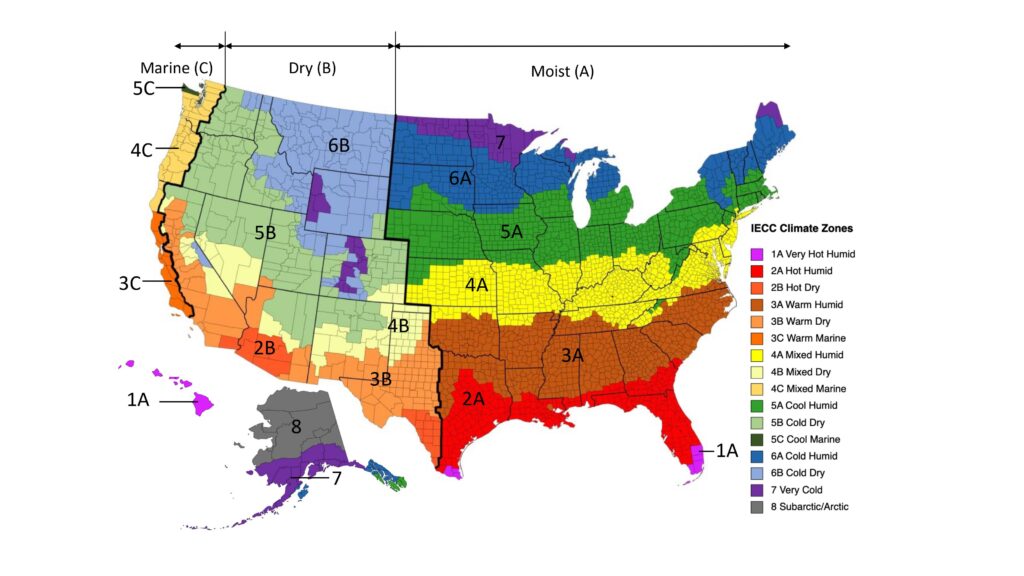
The effectiveness of thermal mass construction varies depending on the climate region. Here’s a breakdown of how thermal mass benefits differ across different climates:
Colder Climates (Heating Emphasis)
- Thermal mass is most valuable in regions with long heating seasons, typically found in IECC Climate Zones 4 and higher.
- Cold climates benefit the most from thermal mass due to the need for temperature regulation and resistance to cold snaps.
Hot-Dry Climates (Cooling Emphasis)
- Hot-dry climates with extended cooling seasons can greatly benefit from thermal mass, particularly when dealing with extreme heat conditions.
- In regions where the outdoor temperature significantly exceeds the indoor temperature during the day and drops well below it at night, thermal mass is highly effective.
- An ideal location for thermal mass in hot-dry climates has an average 24-hour temperature swing of 25°F or more during the summer.
Mixed-Dry Climates (Balanced Heating and Cooling)
- Mixed-dry climates, characterized by substantial heating and cooling seasons, also benefit from thermal mass construction.
- These regions typically experience significant temperature swings during the day and night, making thermal mass a valuable asset for temperature regulation.
Warm-Humid Climates (Limited Benefit)
- In warm-humid climate zones (IECC Climate Zones 1A, 2A, and much of 3A), relying solely on passive cooling strategies with thermal mass is not recommended.
- These climates have less pronounced temperature swings and may not derive significant benefits from thermal mass.
Specific Climate Zones
- Many locations in IECC climate zones 3B, 3C, 4B, and 5B (portions of Hot-Dry, Mixed-Dry, Marine, and Cold-Dry climate regions) exhibit ideal conditions for thermal mass due to high cooling design temperatures and substantial daily temperature swings during the summer.
- Example cities with these conditions are listed in Table 1 below.
Table 1. Example Cities with Ideal Conditions for Thermal Mass:
State City 1% Cooling Design Temp. (°F) Average Summertime Daily Temp. Range (May-Aug) (°F) Climate Zone
Arizona Flagstaff 93 >26 5B
Nogales 98 >24 3B
Kingman 100 >25 3B
Prescott 92 >24 4B
California Barstow 107 >27 3B
Livermore 95 >24 3C
Chino 98 >25 3B
Nevada Carson City 91 >26 4B
Tonopah 93 >28 4B
Fallon 97 >29 5B
Caliente 97 >32 4B
Texas Pampa 97 >24 4B
Dalhart 97 >26 4B
Marfa 91 >25 3B
*Note: The "1% design temperature" is used when designing HVAC systems, representing outdoor temperatures exceeded for only 1% of the year, with a constant indoor temperature of 75°F. Regions with higher daily temperature swings benefit most from thermal mass construction.
Understanding your climate zone and its specific characteristics is essential for effectively implementing thermal mass construction to enhance energy efficiency and comfort in your building.
Retrofitting Thermal Mass Construction in Existing Homes
While incorporating thermal mass construction is most effective during the initial home construction, there are retrofitting opportunities to enhance an existing home’s thermal mass properties. Here are some retrofit options to consider:
- Exterior Wall Insulation: If your home’s concrete walls are uninsulated, consider adding insulation to the exterior. This can improve the thermal performance of the walls and enhance their thermal mass properties.
- Extra Drywall Layer: Adding an extra layer of drywall throughout the house can increase the overall thermal mass of the interior walls. This extra mass helps stabilize indoor temperatures.
- Plaster Finish: Applying a plaster finish to interior walls not only adds thermal mass but also provides a visually appealing and textured surface.
- Tile on Walls and Floors: Installing tile on walls and floors can increase the thermal mass in specific areas of the house. Tile has good thermal conductivity, making it suitable for this purpose.
- Exposed Slab: If your home has a concrete slab foundation, consider removing existing flooring materials and staining the concrete to create a finished floor. This exposes the thermal mass of the slab, which can help regulate indoor temperatures.
- High-Mass Countertops: Installing countertops made of high-mass materials, such as concrete or stone, in the kitchen and bathrooms can contribute to the overall thermal mass of the home.
- Phase Change Material (PCM) Products: Incorporating PCM products into your home can be an effective way to add thermal mass. PCMs can absorb and release heat to help maintain a comfortable indoor environment.
Compliance with Codes and Standards
When incorporating thermal mass construction into your building project, it’s essential to adhere to relevant codes and standards. Here’s an overview of compliance requirements from various codes and programs:
DOE Zero Energy Ready Home (Revision 07)
- Exhibit 1 Mandatory Requirements:
- Item 1) Certified under the ENERGY STAR Qualified Homes Program or the ENERGY STAR Multifamily New Construction Program.
- Item 2) Ceiling, wall, floor, and slab insulation must meet or exceed 2015 IECC levels and achieve Grade 1 installation, per RESNET standards. Refer to the guide “2015 IECC Code Level Insulation – DOE Zero Energy Ready Home Requirements” for detailed information.
2009, 2012, 2015, 2018, and 2021 International Energy Conservation Code (IECC)
- Section R402.2.5 (2012-2021) / R402.2.4 (2009): Mass walls must meet specific criteria, including materials like concrete block, concrete, insulated concrete form, masonry cavity, brick, adobe, and more. Additionally, any wall with a heat capacity equal to or greater than 6 Btu/ft² x °F is considered compliant (2015-2021).
- Section R402.2.9 (2021) / R402.2.10 (2012-2018) / R402.2.8 (2009): Slab-on-grade floors with a floor surface less than 12 inches below grade must be insulated in accordance with specified requirements.
- Section R402.2.9.1 (2021) / R402.2.10 (2012-2018) / R402.2.8 (2009): This section provides specific guidelines for the installation of vertical, under-slab, or horizontal exterior insulation.
- Table R402.1.3 (2021) / R402.1.2 (2015–2018) / R402.1.1 (2009-2012): This table outlines minimum R-values for insulation and fenestration requirements by components, including those related to mass walls.
2009, 2012, 2015, 2018, and 2021 International Residential Code (IRC)
- Section R606.2: Discusses conformance and compliance requirements for various masonry units, mortar, grout, and masonry bonding patterns.
- Section R606.3: Covers construction requirements, including joints, masonry unit placement, wall ties installation, reinforcement protection, grouting, and more.
- Section 606.4: Addresses the thickness of masonry components, including provisions for minimum thickness, rubble stone masonry walls, changes in thickness, and parapet walls.
- Section R608: Focuses on exterior concrete wall construction, including concrete materials, form materials, reinforcement installation, and form ties.
- Sections R606 – R611 (2009 and 2012 IRC): Provide comprehensive guidelines for masonry construction.
Ensuring compliance with these codes and standards is crucial to guarantee the safe and effective implementation of thermal mass construction in your building project. For detailed code language and precise requirements, it is advisable to refer to the relevant codes and standards.
High-thermal-mass construction represents a promising path toward energy efficiency and enhanced comfort in buildings. By incorporating materials with high thermal mass, passive heating and cooling strategies, and thoughtful design, you can significantly reduce your reliance on mechanical heating and cooling systems.
For immediate service or consultation, you may contact us at Allied Emergency Services, INC.
Contact Information:
- Phone: 1-800-792-0212
- Email: Info@AlliedEmergencyServices.com
- Location: Serving Illinois, Wisconsin, and Indiana with a focus on the greater Chicago area.
If you require immediate assistance or have specific questions, our human support is readily available to help you.
Disclaimer: This article is intended for informational purposes only. For professional advice, consult experts in the field.